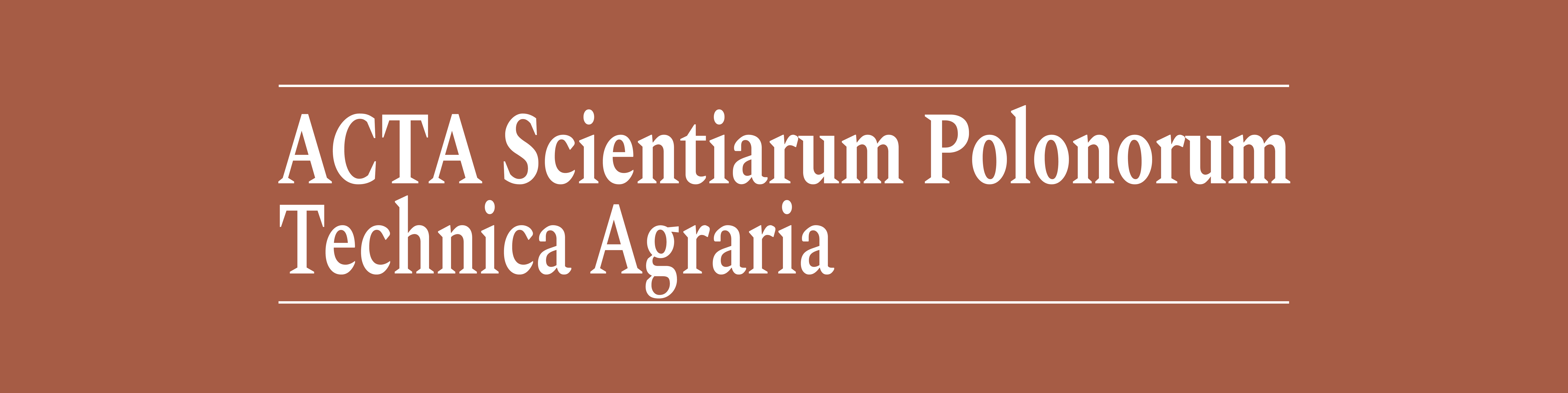
Attempts to reduce net CO2 emission and to increase the use of sustainable materials pose great challenges at the interface of chemical engineering and agricultural engineering. One of the products involved is thermoplastic starch that can partly substitute synthetic plastics, amongst others in packaging. In a first step a semi product is produced by mixing starch and a polyol in a cooking-extrusion process. The material obtained can than be used in other polymer processes, like extrusion, film blowing and injection moulding. Films with thicknesses of 200 µm can be achieved if gelatinisation is good and moisture content constant. In injection moulding shape stability can be retained by a judicious combination of moisture content and process temperature. The final objects can reach a strength comparable to commercial packaging plastics, like polystyrene.
A problem that still exist is the sensitivity of the material to ambient moisture, both at short terms during production as at long times during usage. These problems increase with increasing surface to volume ratio of the final product like, for instance, films. Technologies where the material is coated or where the lubricant is immobilized have to be investigated
to expand the use. From economical point of view it can be expected that the costs of the extra extrusion step during manufacturing of the semi-product can easily be covered by the price difference between starch and synthetic packaging plastics, like polyethylene, polypropylene or polystyrene.
You may also start an advanced similarity search for this article.